Automatic transmission GM 6T: A Rebuilder’s Joy
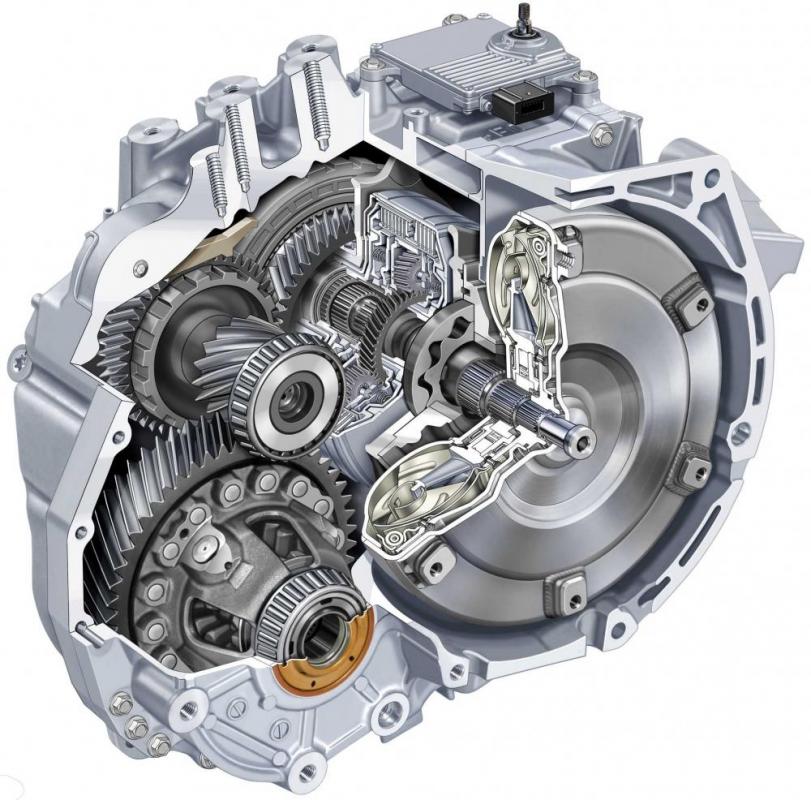
A series of 6-speed transmissions for vehicles with transversal engine mounting was a joint project of General Motors and Ford. They first appeared on the market in 2007. This family includes units intended for the transfer of different torques, which makes it possible to install them on vehicles of various classes. Most transmission models are designed for front-wheel drive, yet there are modifications that are used in all-wheel drive vehicles: the Cadillac SRX (since 2010) and the Opel Captiva (since 2011).
Despite the simple design, these transmissions will eventually develop certain problems. Sometimes these issues occur due to the faults of the design, but even more problems arise from careless and negligent operation. I divided all the troubles into three groups: mechanical failures, hydraulic issues and electronics problems.
Mechanical failures GM 6T
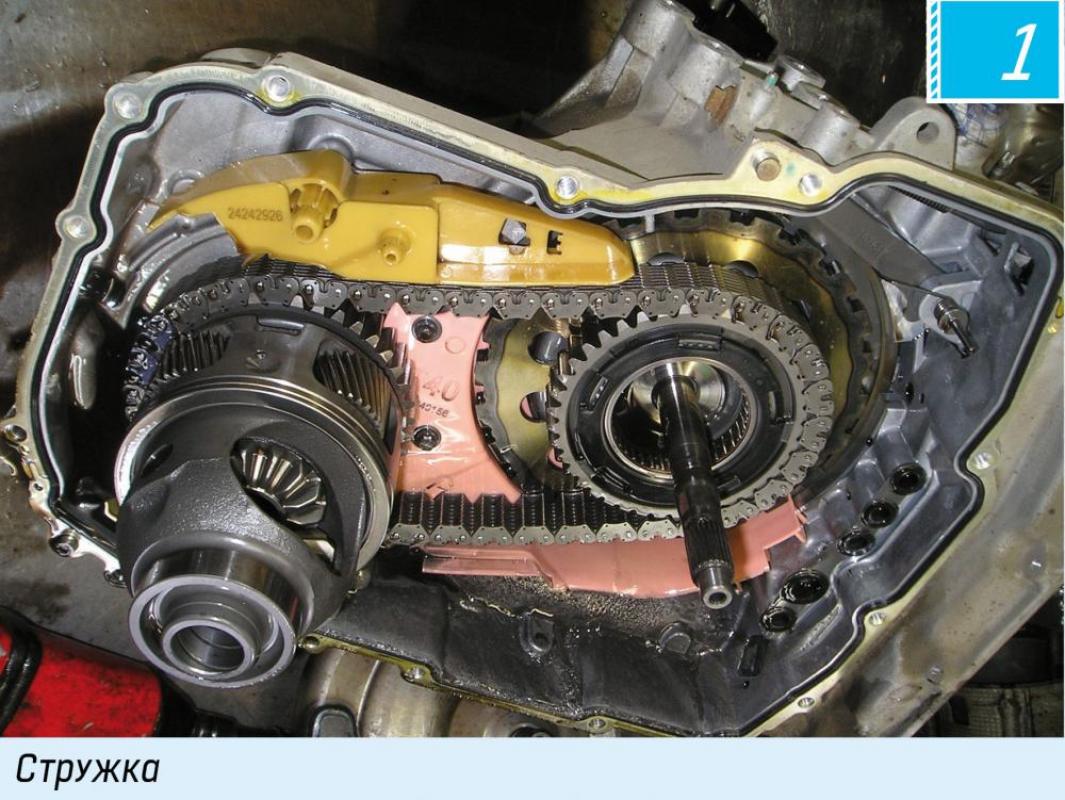
A typical example of a mechanical failure is the “absence” of 3rd and 5th gears, as well as the reverse gear. As a rule, when you remove the transmission, you discover a huge amount of metal filings (1). You can see it even without disassembling the unit, but simply pulling out the input speed sensor (ISS), even if it’s still attached to the wire leading inside the unit (2). If there’re a lot of filings on this sensor, the spring plate has probably fractured (3). Its breakdown leads to an increased length of piston stroke, which, in its turn, by shock turning-on, knocks out the retainer ring from the 3-5-R pack (4), and may cause further breakdown, as luck would have it. The fragments can get into the planetary reduction gear and make havoc inside, they can also cut up the gear teeth (5), or even fly all the way to the free wheel (a mechanical diode), so it either splits or gets jammed with metal filings (6, 7). Sometimes it happens so that the parts are impossible to separate and you have to pull them out as a single unit (8). In some cases you cannot take it to pieces without breaking. In the pictures you can see elements that often get damaged due to such failures (9).
The worst part is that the tiny particles of metal can escape through the filter and cause the burring of the pump (both the pump case and its other parts and valves) in the valve body, leading to the solenoid jamming. In many cases, the transmission case also gets damaged in the area of the 2-6 gear piston (10). We’ve had an instance when the case was cut through by the spring plate (11).
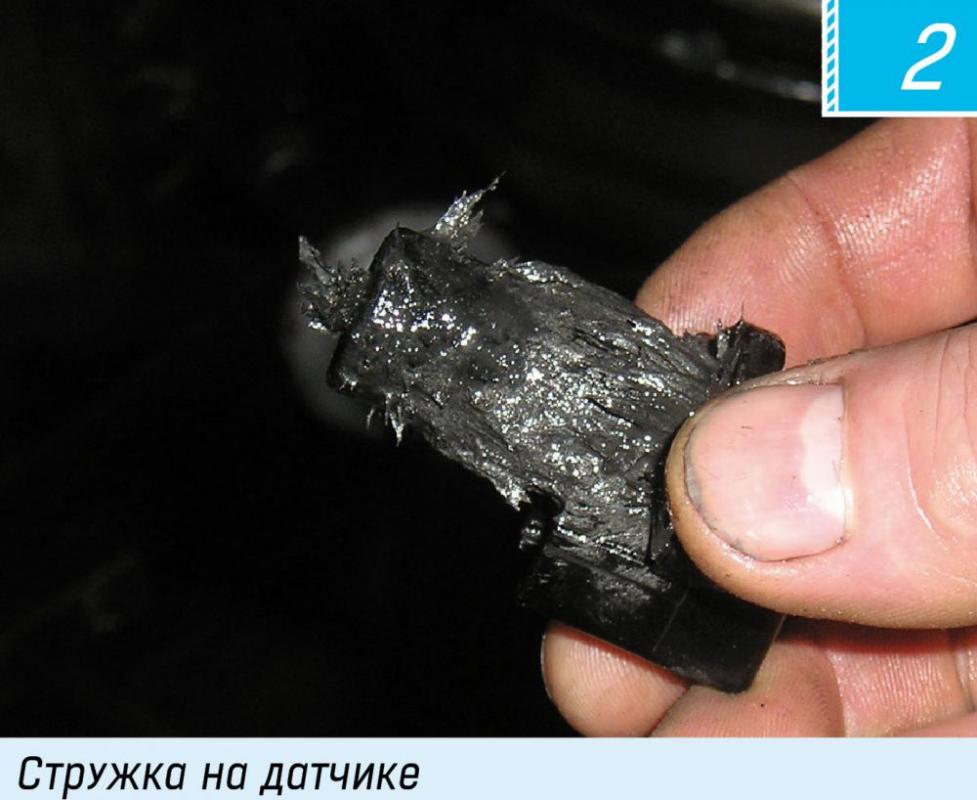
However, had the driver been more careful, severe consequences could have been avoided. After the spring plate splits, a perceptible kick appears when shifting into reverse. If you cease operation of the car at this moment you may be able to avoid grave consequences. But, as a rule, the owners drive to the last, until the car “dies” on them, and the dealers don’t want to get involved either – all the gears are present and there’re no DTC-s – so, according to them, everything is fine.
The rebuilding process would mean the replacement of damaged parts. Besides, it’s necessary to check the pump, the valve body (covered in detail in the Hydraulics section) and clean, or even replace, the solenoids.
The second most common mechanical failure is the differential trouble, and it also results from improper operation. Those who like wheel-spinning and dart off from the spot get the differential pinion shaft to turn through (which may happen in other transmissions as well) (12). Sometimes it sticks out of the differential so far as to break through the case making a hole in it.
Oftentimes, the bushing in the transmission case gets damaged too (13, 14, 15), and the inner CV joint gets loose. This problem is indicated by an oil leak which is not eliminated by a seal replacement.
On AWD vehicles the differential cover bolts get unscrewed. Sometimes they break off and their fragments start travelling inside the transmission, crashing everything on their way – and in this case nobody will say how it all will end. At times they punch through the case (16) – it mostly happens in early model units. If during disassembly you see a differential with a removable cover, make sure you unscrew all the bolts and tighten them up again with a thread locker. On later models the differential is a non-assembled, one-piece unit.
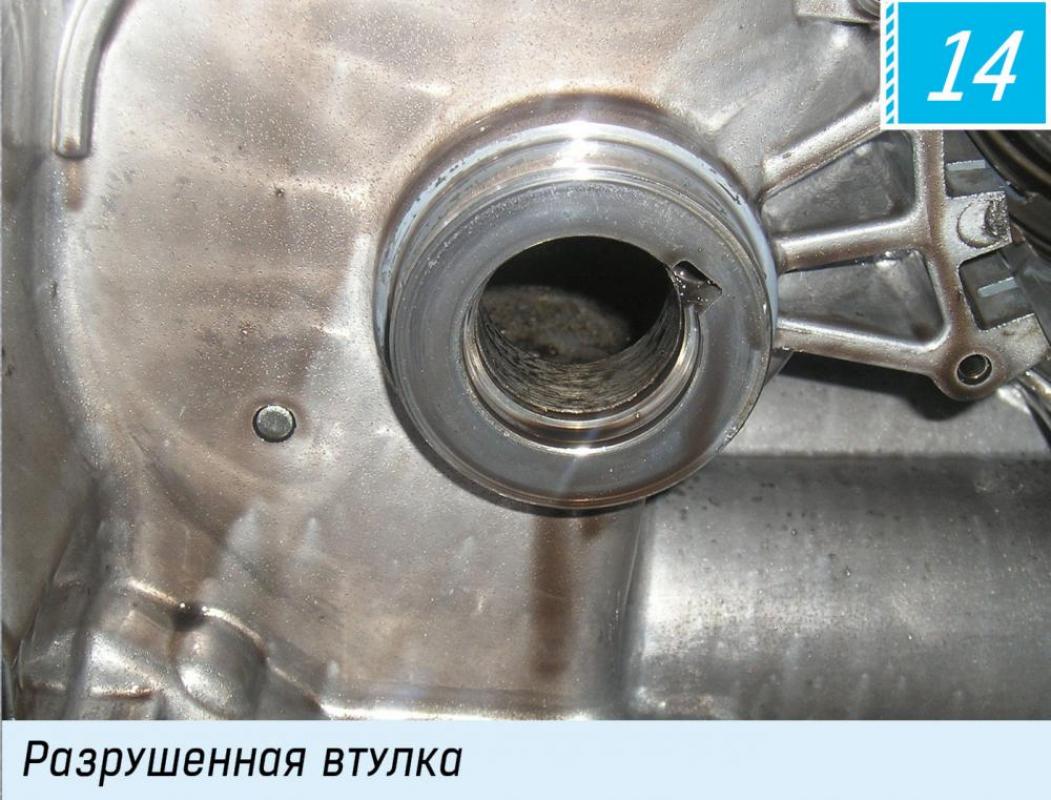
The bearing surface area grinds away (17). This happens in both dismountable and non-dismountable differentials. Sometimes you manage to avoid its replacement by shifting the bearing in the case in such a way as to make it work on the unworn part. In other cases you’ll have to melt some part of the damaged surface, then grind it off and heat-treat it. Another solution is to replace the cover (on the dismountable differential) or the differential itself (if it’s non-dismountable).
In many cases, the mounting bearing on the transmission case gets damaged: it kind of presses through the bearing surface. When this is the case, the differential end play increases and a perceptible kick occurs when shifting R-D-R-D… As a result, the chain comes into contact with its guides, and they develop wear scars (18), which further leads to the breakup of the guides (19). This problem can be eliminated by the installation of washers, turned to the required thickness.
Practically every transmission after long operation has a crown gear end play. The effect is the same as for the previous problem. The “cure” is simple – the installation of a ring, turned to the required size.
Sometimes the free wheel (the mechanical diode) (20) destroys by itself. In this case the car loses speed when shifting 1-2, as if someone presses the brake pedal. Oftentimes, 2-6 gear frictions burn as well – in this case, only their replacement will help.
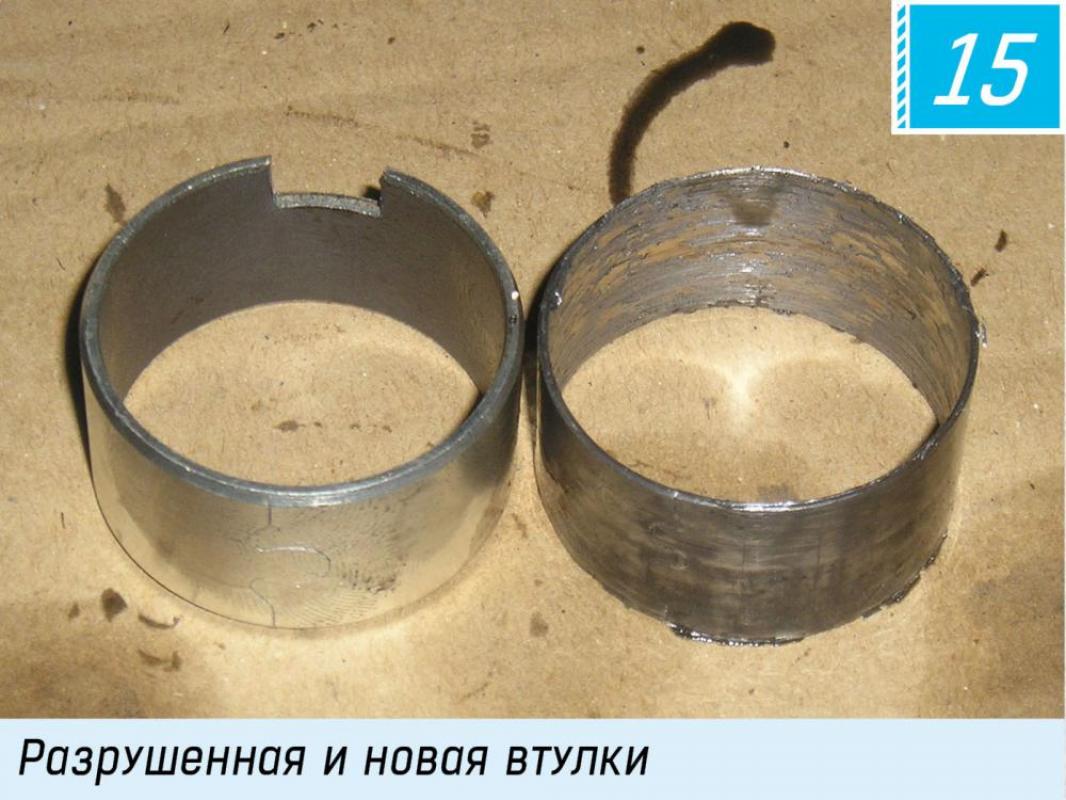
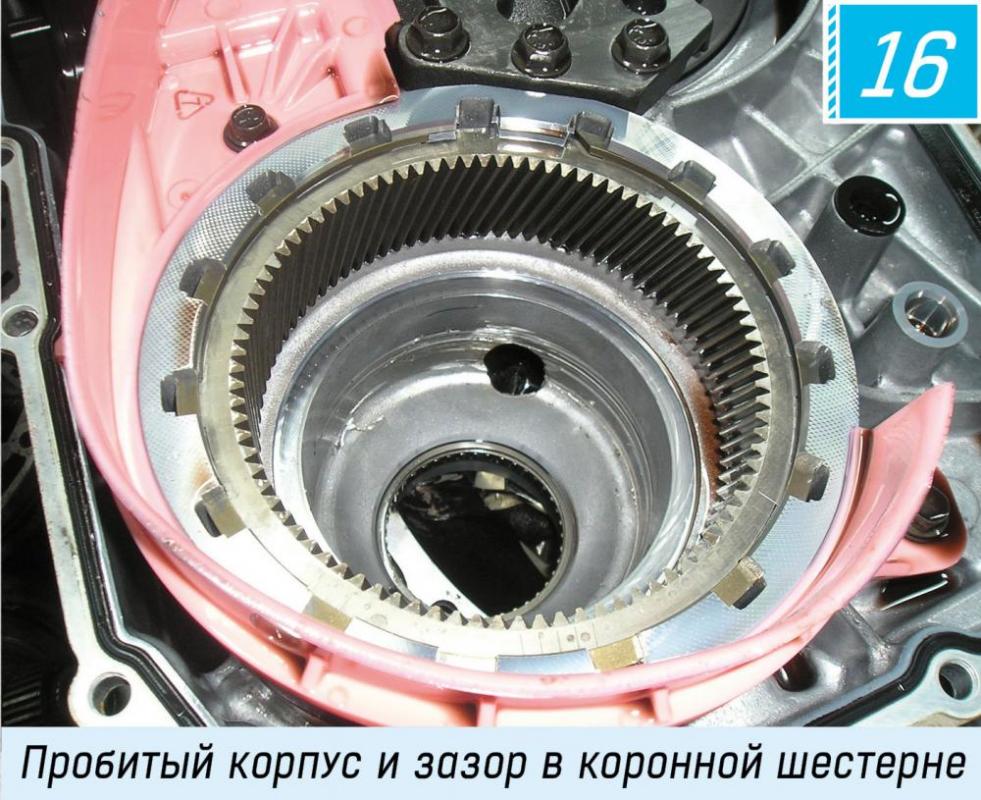
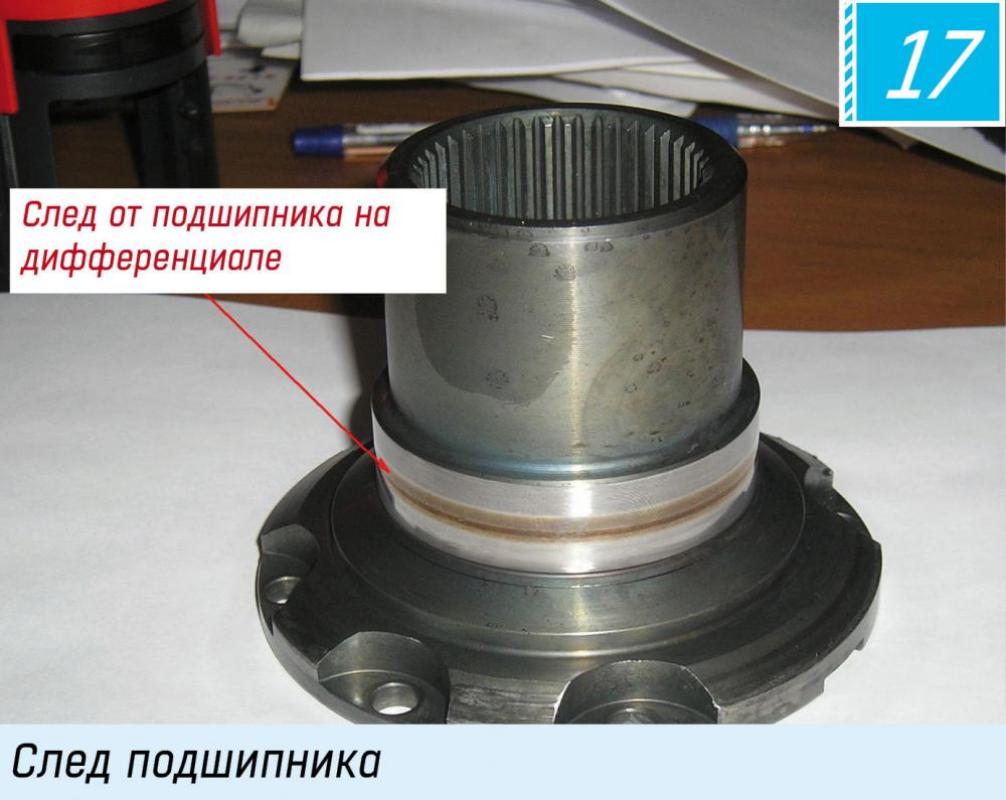
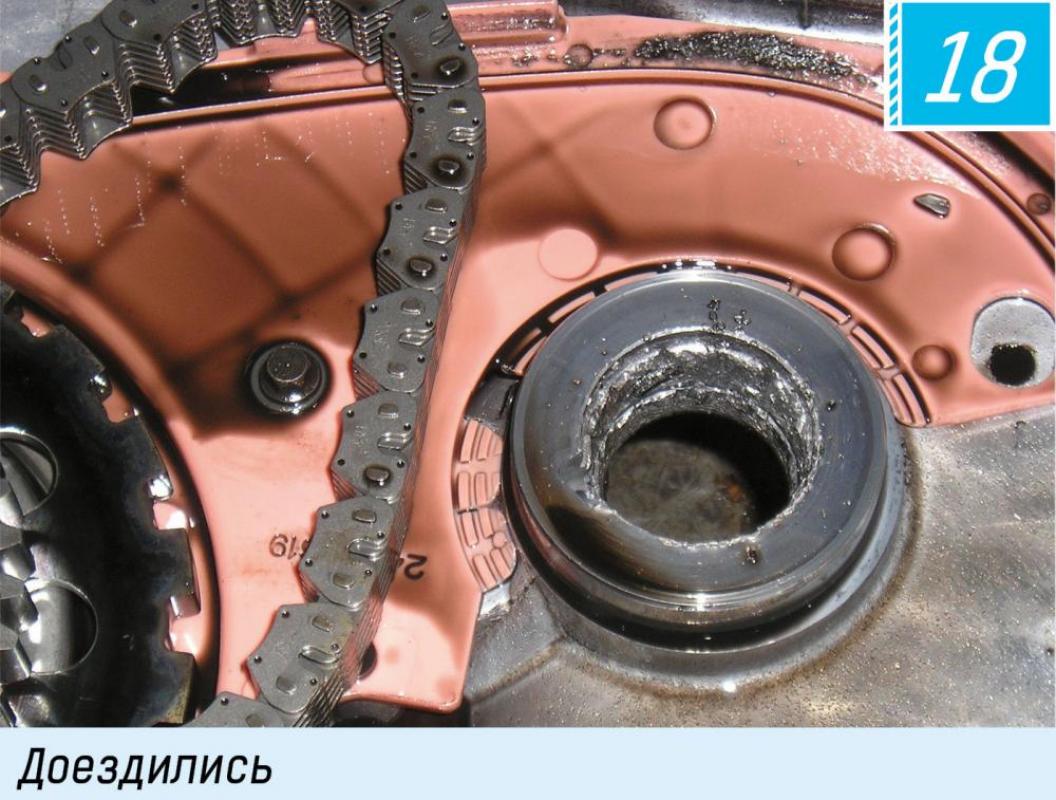
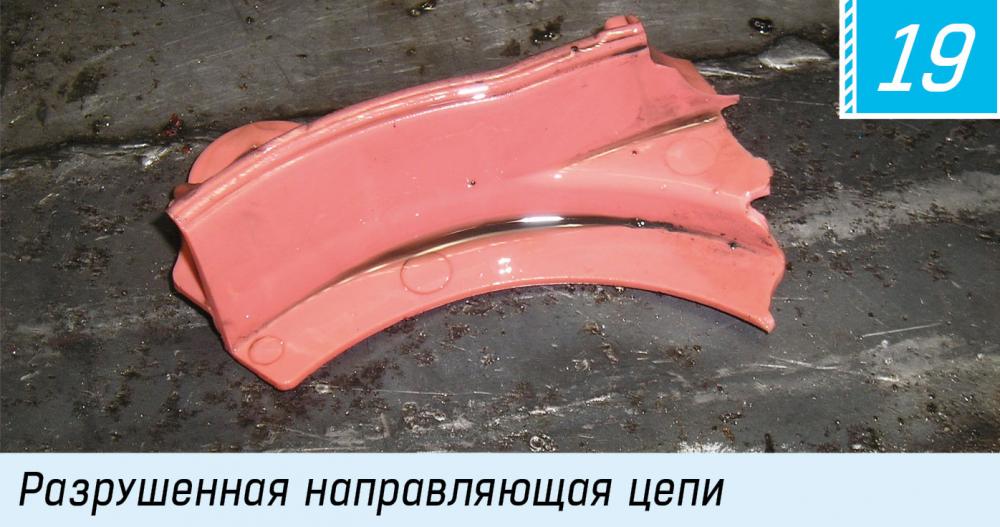
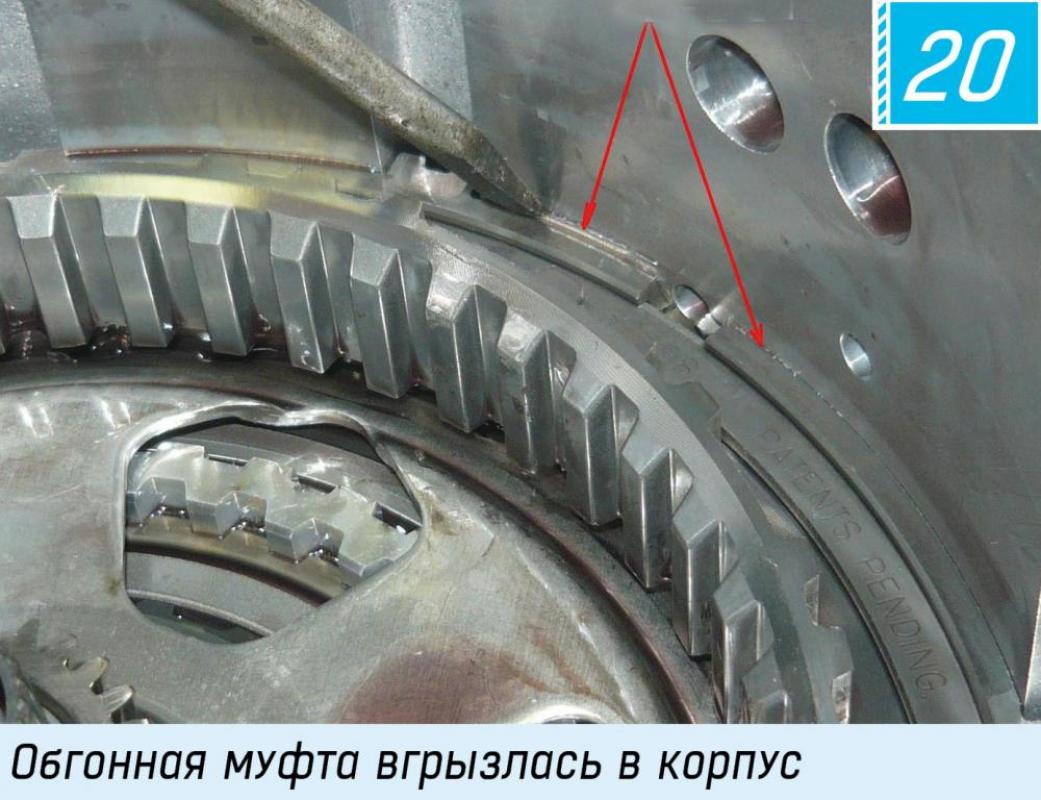
Hydraulics troubles GM 6T
When rebuilding a transmission of this type you must always check the condition of the bushings. On “large” transmissions (6T40/45/50/75), with the mechanical part in tatters, the bushings may still remain in an operational condition, whereas in 6T30, even if the transmission itself is in quite a decent condition, the bushings will in most cases be a real mess. We would like to thank our Krasnoyarsk counterparts for eliciting this correlation.
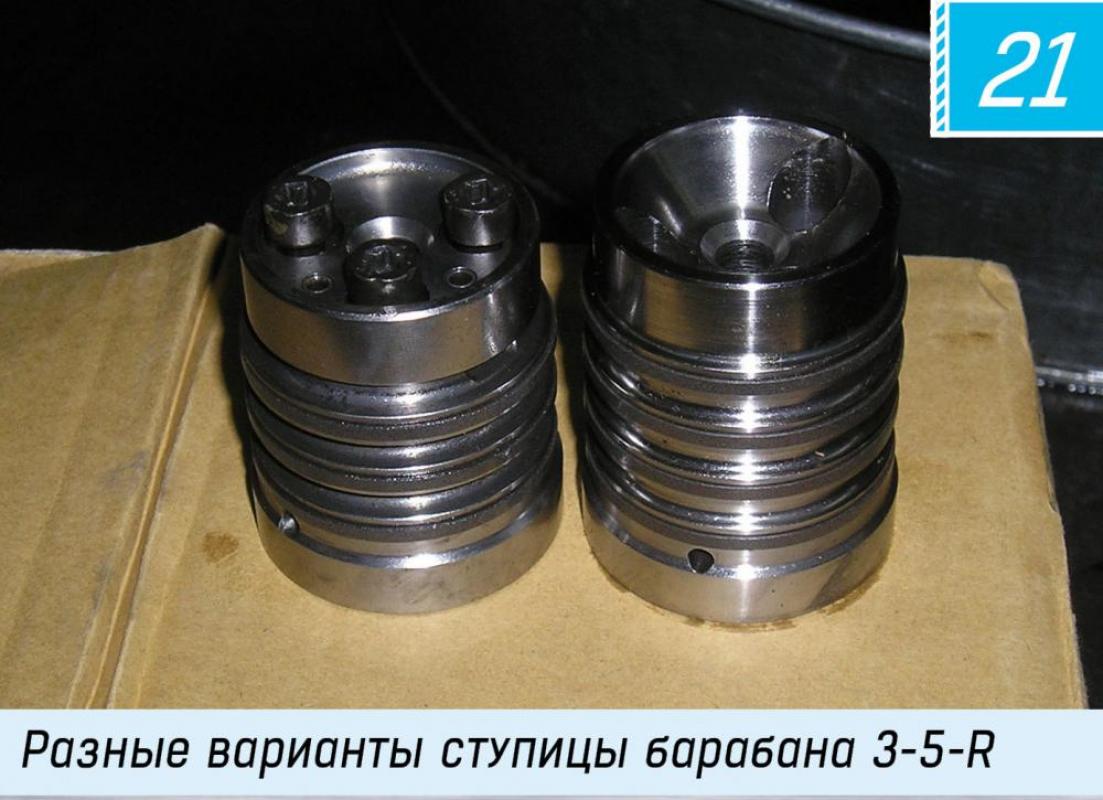
If while driving you feel a prominent kick at 1-2 and 2-1 shifts, the problem is most likely to be in the 2-6 gear piston. Here, rubber can peel off, or sometimes the piston drain port becomes clogged with dust particles or wear products. Speaking of this port – the instruction manual goes: the piston must be installed so that the port faces 12 o’clock – or, in other words, it should be right on top. But no matter how many transmissions we have disassembled – in none of them did we see a piston installed in the correct position. Once we even disassembled a unit that had been rebuilt by our own company some time before – and the piston had already become unseated. So, we can conclude that the piston does turn a little bit while in operation. The steel discs fetch away in their grooves and, obviously, when they get loaded they turn the piston. This happens due to the absence of any catcher.
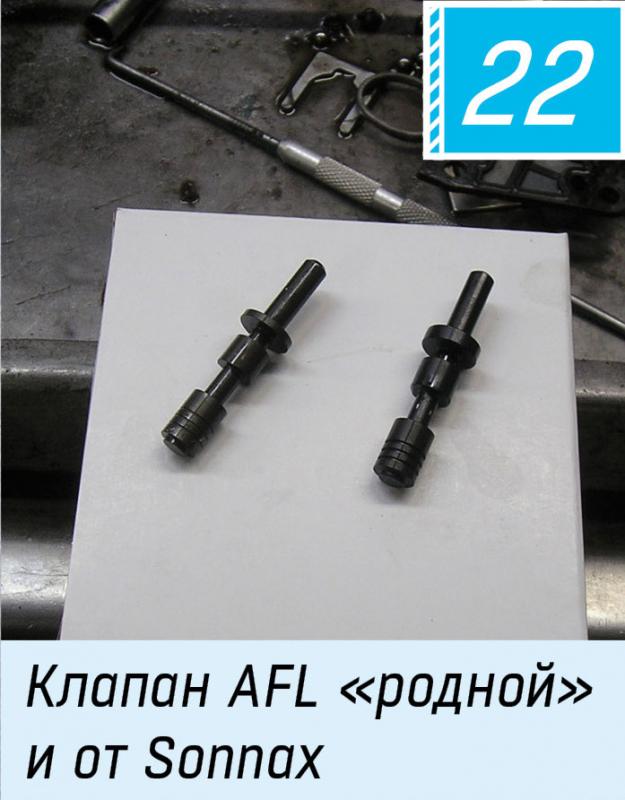
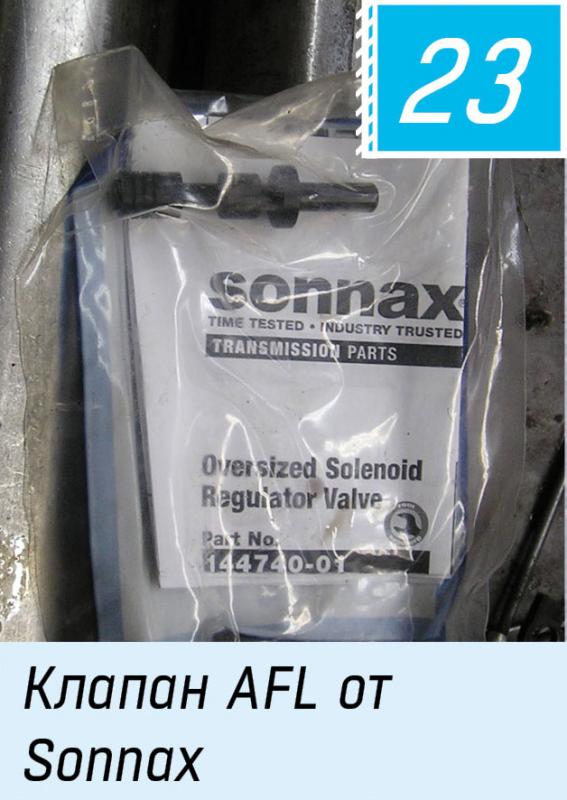
In Gen. II, the 3-5-R drum hub has three teflon rings, not four (21). According to our observations, the three-ring kit is less reliable in operation that the four-ring one. These units are interchangeable: you can install the four-ting hub instead of the three-ring one. But you need to replace the unit as a whole – the drum and the hub assembled.
Valve body troubles are not uncommon to 6T as well. A typical situation: a cold car is running perfectly, but as it starts warming up the high gears disappear. In the end you only have 1st and 2nd gears left. After vacuum testing it turns out that some valves don’t pass the test. Sonnax produces several repair valves and special tools, but rebuilding a valve body is not always cost efficient. The price of a new valve body ranges from 11 to 15 thousand rubles, whereas a complete tool kit is much more expensive. That’s why purchasing the tools and service kits only makes sense when you repair such units in large quantities. In our case, however, it’s cheaper to buy a new valve body.
The AFL valve is an exception (22, 23). The valve itself is not expensive and the tools for valve body rebuilding are quite affordable too. And the valve, indeed, either doesn’t pass the test altogether, or does pass it but at the bottom values. Of course, Sonnax produces a Zip Kit for these transmissions as well. You don’t need any special tools for the installation of this kit. But its price is also in the realm of 11 thousand rubles – practically like a new valve body.
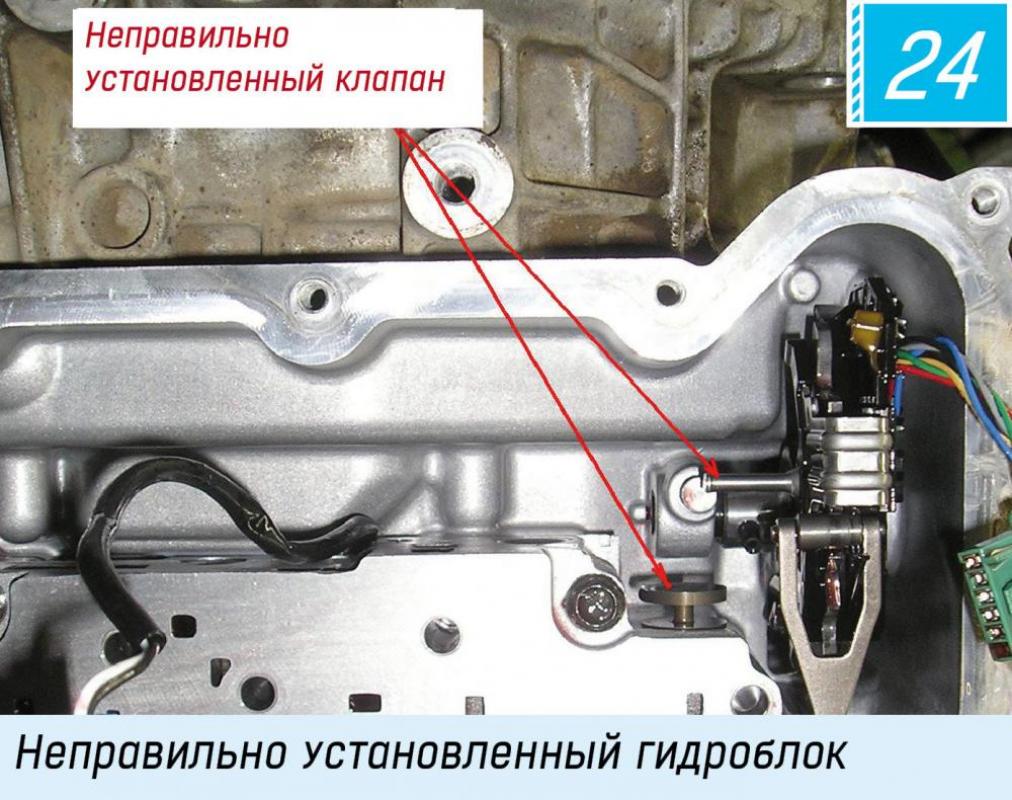
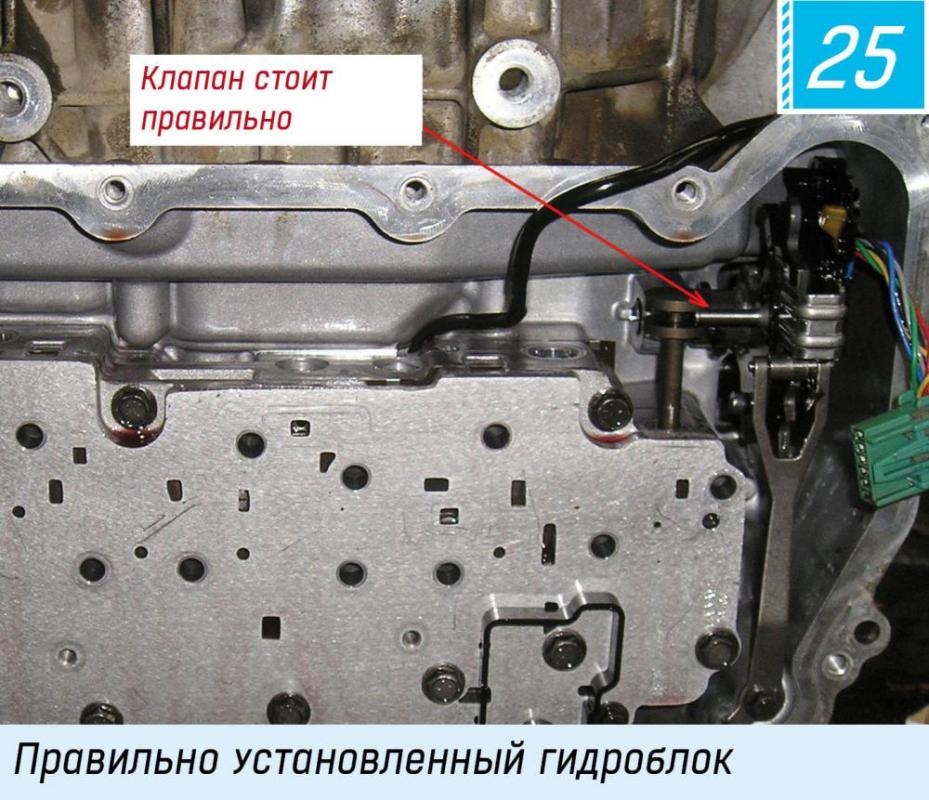
What is really worth buying from Sonnax is a tool kit for repair of the pump valves. Those are the pressure control valve and the lock-up valve. They do, indeed, often get worn. The wear sometimes reaches such a degree when you don’t need a vacuum-tester – you can see it with a naked eye. And the consequences of worn valves are deplorable – the rebuilt transmission will soon get out of order and the client will reappear at your door.
When you assemble a transmission take special care to make a butt-joint of the case halves. There’s a seal on the pump hub which is easy to damage.
Sometimes we get phone calls from dealers: we replaced the valve body and the solenoid assembly (they are usually replaced all together), and after that the vehicle started acting strange – doesn’t go backwards, or, on the contrary, only goes backwards, or doesn’t go at all. If you hear that, you can be 100% sure that when installing the valve body the service men “missed” the right spot for the manual valve and it fell into a random position (24). The repair algorithm is clear – to disassemble the unit and put it back together right (25, 26).
When installing the valve body you must remember: two bolts are shorter than the others and must be put into the proper places (27).
Another hydraulics issue is related to the solenoid assembly. Transmissions of the first generation have pressure sensors. The latter have diaphragms. Sometimes (not often, we’ve only dealt with isolated cases) they rupture, and then there is a leak in the hydraulic circuit. Sonnax has a service kit for the repair of pressure sensors. It has both diaphragms and rubber rings (28). It’s essential to have a kit like that handy when you are rebuilding a transmission. The good news is that it’s available at a very attractive price.
The last, but not least, hydraulics issue: take special care when buying filters. We’ve seen some specimen that literally fell into two pieces along the seam of the adhesive joint. Even if the price is appropriate and the marking is the same as in the good ones – such instances still occur. Now before installing the filter in any type of transmissions we try to “break” it by hand – such a simple reliability test. Only take it easy and don’t apply too much force – we’re all different in terms of arm strength. In fact, we’re not the only ones to have faced this problem, it occurs in filters for other transmissions as well, yet it’s worth mentioning here.
Electronics issues GM 6T
The electrical part of a transmission includes sensors, solenoids and the electronic control unit (TCM). The two temperature sensors and the pressure sensors (there’re four in Generation I units and none in Generation II) are built into the solenoid assembly, the speed sensors are located in a separate place.
The speed sensors as such are very reliable. In the last several years we’ve only had to replace one failed output speed sensor (OSS). However, after the dealer’s interference problems may arise. The truth is that the OSS wire must be laid in a particular way, but the dealer’s employees (and not only them) after removing the valve body and the solenoid assembly, don’t lay the wires properly (29). As a result, the wire can get squashed either by the valve body or its cover (30). There have been cases (albeit isolated ones) when the short circuit lead to a TCM failure, but more often the Check engine lamp comes on and the transmission won’t shift higher than second gear, besides the manual mode won’t work. Needless to say, a sensor trouble code is registered in the TCM memory. You simply need to check how the wiring is laid and if it’s squashed – replace it.
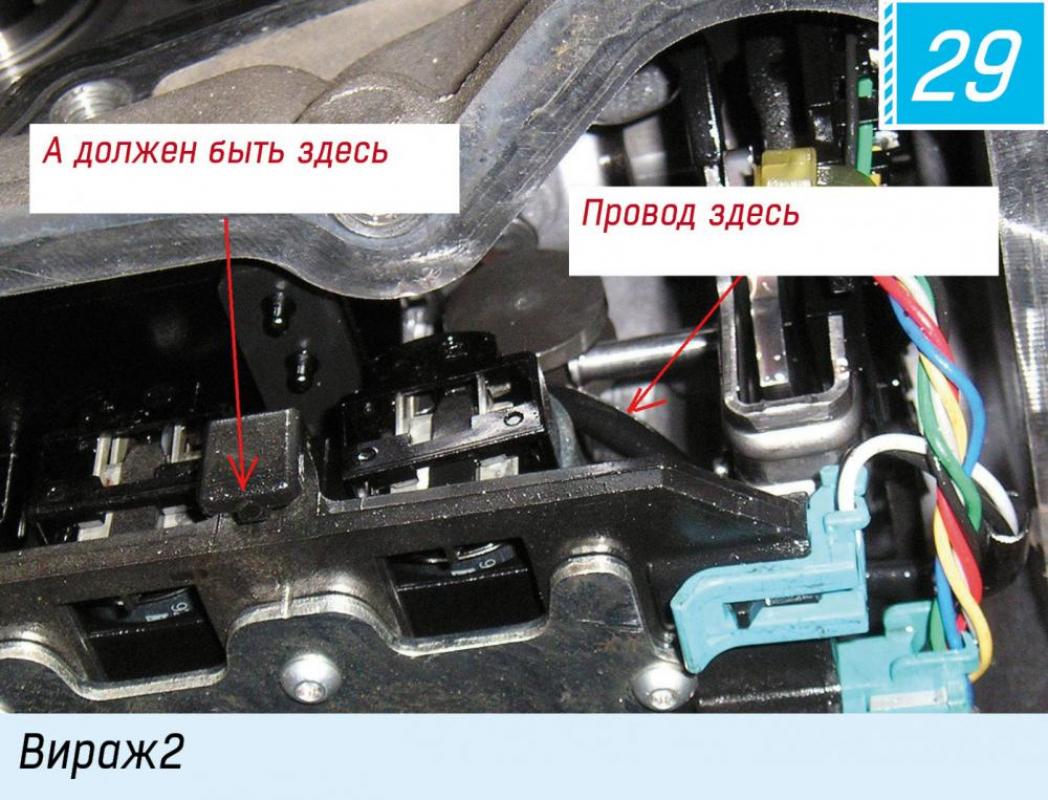
We have never observed troubles connected with the failed electrical part of the pressure sensors. What can happen is a diaphragm rupture, which was covered in the Hydraulics section.
If the client brings you a car which has no forward drive and a Solenoid 5 DTC (the latter may be absent though) – do the following:
- Start the engine (get somebody to sit at the wheel, press the brake pedal and pull the handbrake);
- Shift the gear into the N position;
- Remove the connector from the transmission;
- Check if the forward drive has reappeared.
If the car started moving forward (naturally, in the emergency mode) you can be practically sure that there’s a mechanical failure in Solenoid 5. The electrical part will work properly. The cause of the trouble is the valve seat, which falls out in the solenoid. In the pictures you can see what exactly happens and how to tell a properly functioning solenoid from a faulty one (31, 32).
However, this is not the only problem. A solenoid is an electromagnet, and inside its valve there’s a permanent magnet as well, through which oil circulates. The oil always contains metal particles – wear products. These particles precipitate inside the solenoid and on the magnet, disrupting the solenoid operation. Regular cleaning helps solve this problem.
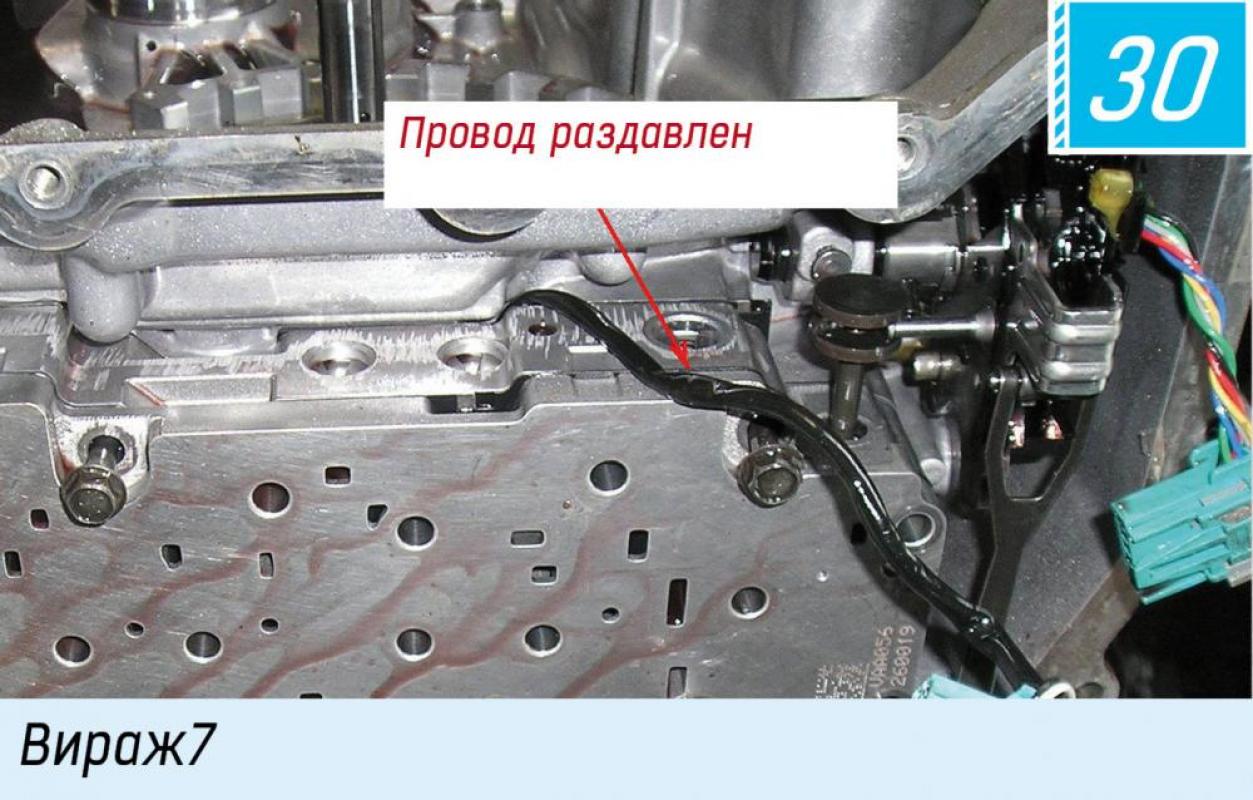
Troubles with the electronic module occur too, but not very often. The most common symptom is a kick at a speed of about 38 km/h when coasting (when it’s slowing down by itself or when you’re pressing the brake pedal lightly). The attempts to “cure” this failure by replacing the solenoids or updating the solenoid assembly have never been successful. You have to replace the whole solenoid assembly.
A common issue for vehicles with this transmission is stumbling and RPM change when standing at a stop-light. You need to do the following: pull the handbrake and release the brake pedal. If the problem disappears the cause is in the auto-neutral. There’re two ways to eliminate this problem.
You can upgrade the TCM with software without the auto-neutral by requesting the VCI-code. But this solution is not available for some vehicles. The replacement of the TCM has been of no help either.
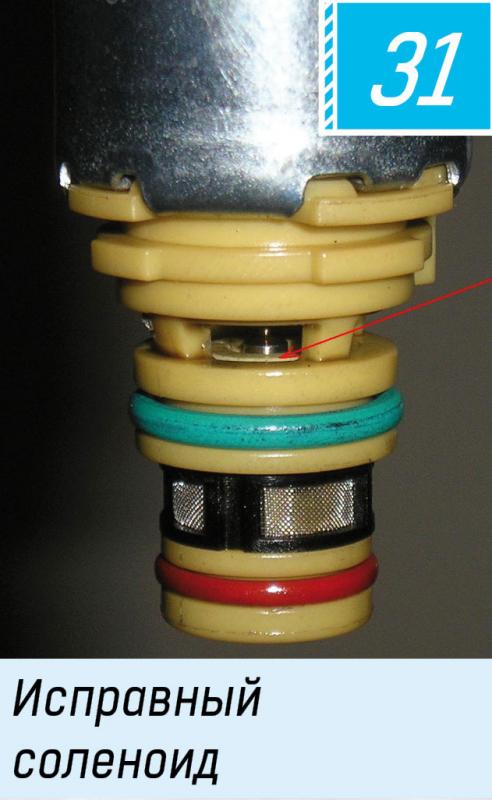
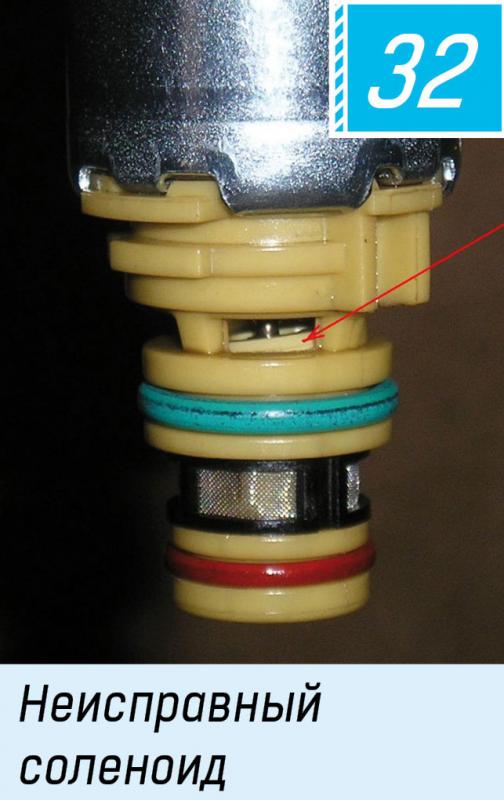
A more complicated but a sure way is to replace the friction plates of the 1234 stack with the ones that have oil grooves. You can even cut these grooves yourself. Besides, you can install new steel discs, or abrade the old ones with abrasive paper, to remove the “glass” effect, making the surface brushed (matted).
General Motors devoted a full-fledged study to this issue. There’s a bulletin with information which discs are to be replaced with which, with the disc catalogue numbers. But we simply installed discs with grooves, removed the “glass” from the steel discs and the problem was solved.
Cleaning of removed solenoids GM 6T
When rebuilding a transmission we always take down the solenoid assembly, test and clean them without disassembling it. To do so we use a special tool which was tailor-made for this purpose. You put a solenoid inside it, fix it with the same clip as in the solenoid assembly, then supply compressed air (in this case – 8 atm), PWM signal (amplitude: 12V, frequency: 50-100 Hz). Changing the duty cycle we monitor the pressure gauge and listen out for the sound that the solenoid produces. The gauge readings must change without fluctuations from 0 to the pressure values supplied on the solenoid, or vice versa, depending on the solenoid type (normally open or normally closed). Remember that the solenoid is polarized, which means that you need to supply the impulses with the correct polarity. If you confuse them, nothing too bad happens, the solenoid simply won’t work at all. In this case you need to swap the wires.
Be prepared for mud to pop out of the solenoid, so dress appropriately. In most cases you’ll hear a loud humming noise. Normally open solenoids are quieter that normally closed ones.
As a rule, a very filthy solenoid produces hardly any humming noise, but a hissing one. As it gets cleaner, the sound becomes louder and clearer. There are times when the solenoid leaks air a little (the pressure gauge readings are ok). But it doesn’t prevent it from working properly. You can calibrate the scale of the PWM-generator regulator in pressure units, using solenoids known to be working correctly. Then it will become easier for you to select solenoids according to their flow capacity. As PWM-generators we used the power regulator MP301F by “Master Kit”. This model is out of production now, so you can take the MP301M and change the frequency-determining chain for reaching the required frequency (originally it is 20 Hz).
And, of course, the easiest solution is to disassemble the solenoids and wash them.
Igor Emelyanov
CEO at OOO ”AT-Service”